The world operates on feedback loops where some, or all, of a system’s output is used as input for future operational adjustments; water and wastewater treatment plants are no exception. The equipment and control systems within a plant all operate using feedback loops, and even the professional plant operators themselves employ feedback loops and decision trees to guide their decisions. From acquisition and analysis (reporting) through to adjustment and monitoring, effective plant operation is not possible without the timely and accurate data that these loops operate upon.
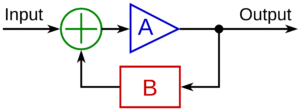
This article delves into an important part of this feedback loop by focusing on the acquisition of treatment plant operational data. It briefly describes our Process Control & Monitoring (PC&M℠) system and explains how the system can be fed by PC&M Connect!. It will also explain how the feedback loop can sometimes extend outside of the treatment plant to help guide a plant owner’s line-of-business decisions.
Plant Data Sources
The ability to capture, store, organize, and report on data is critical for operating water and wastewater treatment plants and these functions are typically the primary responsibility of Supervisory Control and Data Acquisition (SCADA) systems. SCADA systems are vital for monitoring and controlling industrial processes since they help to maintain efficiency, gather and store data for smart operational decisions, and communicate system issues to help mitigate downtime.
SCADA systems are extremely expensive to develop, test, and install, which is why some plant owners opt to rely on simpler, more affordable Human Machine Interface (HMI) systems to control their facilities. HMI systems are more limited in their scope and capabilities and typically do not include the robust data collection and storage features of a SCADA system, but they do offer many of the same control functions.
Because of their importance to the treatment process, access to these systems is strictly controlled and is usually limited to only those who work inside the plant. To shield them from the public Internet, these systems are protected behind firewalls and other security devices, which make data accessibility and portability either extremely limited or impossible.
Even when they are available through highly secure means, like through a Virtual Private Network, accessing SCADA and HMI systems can be quite difficult for anyone who is not an engineer or treatment plant operator. These systems are designed for a specific user audience, which means that navigating to data and manipulating it in a meaningful way can be very challenging.
An Open Facility Data Hub
Designed and maintained by U.S. Water, Process Control & Monitoring (PC&M℠) is an Internet accessible, digital hub that encapsulates everything about a treatment facility. Along with a file repository for permits, standard operating procedures, and other treatment process documentation, the system also stores operational treatment process data making it easily accessible to anyone who needs it. Even more helpful, this data can be combined with other data sources, like maintenance, production, and building management systems, to reveal helpful insights in the form of tables, graphs, and interactive charts.
For unique customer needs, custom point-in-time and historical trend reports can be created with color coding and color banding to make the information easy to understand and interpret. PC&M allows users to subscribe to their favorite reports so they are automatically emailed to them whenever new data is posted – without the need to log into the system. Users can also receive text alerts when discrete parameter values exceed preset thresholds.
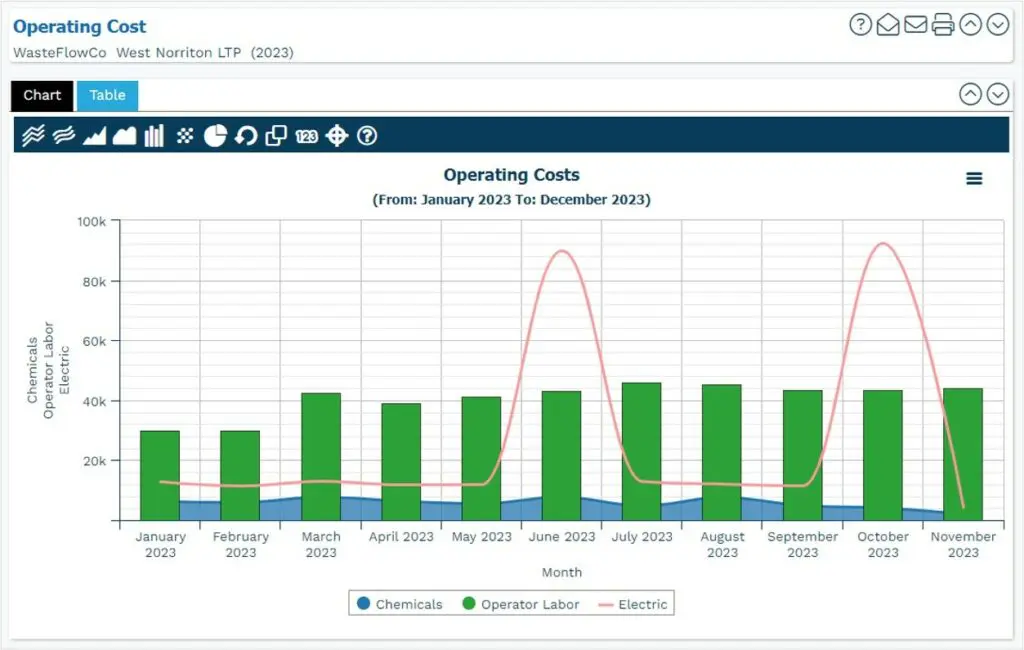
When a “canned” custom report does not exist, the AdHoc feature can quickly prepare a dynamic chart with a combination of data parameters in just a few clicks. Any table or chart can be exported into various formats, which makes it simple to leverage data for your business presentations and reports.
For external data sets that are extensive and voluminous, it doesn’t make sense to duplicate them within PC&M so your internal data mining warehouses, business intelligence systems, or dashboard visualization platforms (e.g., Microsoft PowerBI) can pull operational data from PC&M upon request using our standards compliant application programming interface.
Getting Data into PC&M
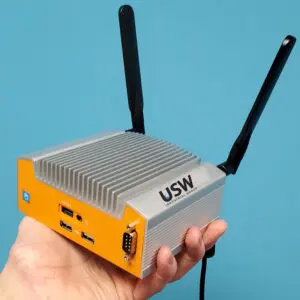
When it comes to data acquisition, it’s best to capture data automatically and directly from the source that generates it, and that’s exactly what PC&M Connect! does. PC&M Connect! is a small form factor data appliance that resides on a treatment plant controls network. By leveraging Modbus protocols and the OPC standard, it collects data from sensors, program logic controllers (PLCs), and other digital and analog instrumentation, and temporarily stores this information within its local database. Then it periodically uploads its internal data store to a private Internet cloud database where it is subsequently aggregated and ingested into the PC&M application database.
Unlike human captured data, PC&M Connect! processes direct-source data that is completely free of transcription errors. The process is performed repetitively resulting in a continual data feed, which is not the case with manual capture, especially at sites that are only manned periodically.
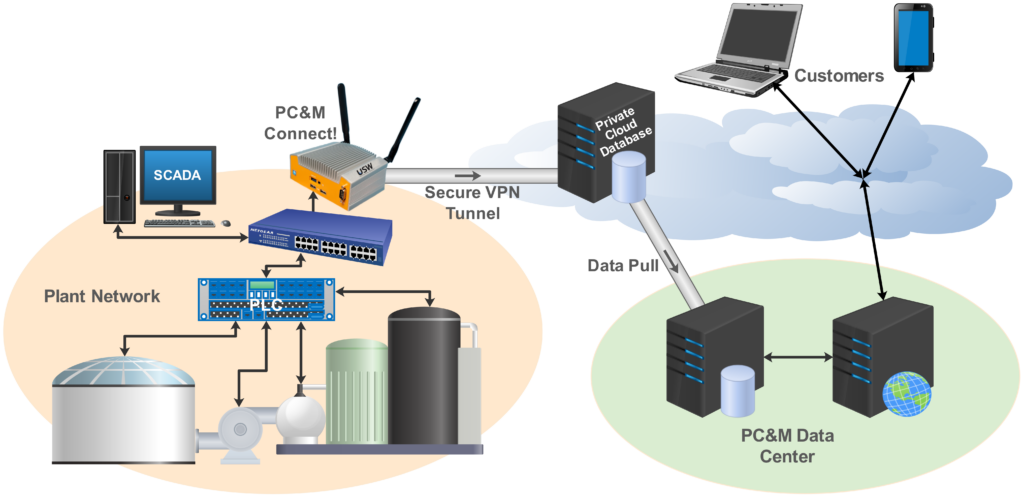
With an investment of just a few thousand dollars, the base PC&M Connect! package can be custom-programmed to capture up to 50 data points, and the number of points can be expanded for an additional fee. There are no recurring costs. The solution can grow as equipment is scaled out and configuration changes can be performed remotely to save travel costs.
Connectivity to the cloud is established through a secure virtual private network that eliminates the possibility of data interception while in transit. And even though PC&M Connect! has access to sensitive plant infrastructure, cyberattacks can be eliminated using an optional Modbus bridge that maintains a serial, non-routable communication path into the plant network.
An optional data analytics dashboard can be created to surface more granular data than what is supported by PC&M. This is especially helpful for customers who require a detailed data picture but lack an operating SCADA system.
Benefits of PC&M Connect!
With seamless integration, PC&M Connect! offers these compelling benefits:
- Efficient – Manual data entry time is eliminated reducing labor requirements.
- Accurate – Direct capture from instrumentation eliminates typographical errors that may be common with manual capture.
- Comprehensive – Data is continually captured 24/7 providing complete data coverage and avoiding gaps from unattended manual entry.
- Secure – Dual network cards, unique subnets, and optional non-routable serial bridges isolate the plant network from the Internet.
- Safe – Does not interfere with SCADA, HMI, or other plant equipment. PC&M Connect! captures sensor and PLC data while it is communicated over the plant network.
- Resilient – Using its store and forward capability, data is retained when Internet connectivity is lost and is pushed once communications are reestablished.
Closing the Loop
Effective treatment plant operations is only possible with timely and accurate data and PC&M Connect! makes that a reality. For a modest investment, instrumentation data can be acquired from its source and fed into the feedback loop that is employed by professional plant operators who use the online PC&M system to guide their treatment process adjustment decisions. Extending the loop outside the plant, system-to-system integration can be established with your internal business processes and reporting systems by leveraging our application programming interface.
Contact your U.S. Water operations manager today to learn more about how the operation of your treatment plant can be significantly improved with the addition of PC&M Connect!.